-
Custom Strut Tower Bracing
Hey all!
While I am working on random little issues with my Beat I wanted to take some time to start modifying it to make it even more awesome. First up was an attempt at a custom strut tower brace to see the ease with which I can start fabricating chassis strengthening components. My day job is as a prototype fabricator and shop manager for an industrial design firm which means I have access to a full wood and metal shop complete with CNC mill and a bunch of other toys. So I figured this would be a good test project for Beat modification.
I have found a variety of different bracing components available and every single one of them looks pretty easy and straight forward to fabricate so being the frugal guy that I am I challenged myself to start replicating them and making the Beat just a little better, one piece at a time. The choice for the front strut tower brace build was due to accessibility and ease of design. So here is how that project went!
First off I took a variety of measurements and input them into Solidworks to create a paper test template.
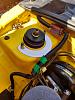
Then after I knew the dimensions were decently accurate I refined the shape of the base plate to accommodate the upright support structure that would bolt to the cross bar.
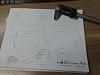
I then took the new templates and spray mounted them to a sheet of .12" steel (3mm). I center punched the hole locations, scored the cut lines (just in case the paper came off during cutting) and began drilling.
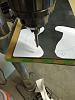
Once completely drilled I parted the pieces off from the larger sheet and separated them from each other to better maneuver them while cutting out the final shape.
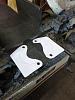
I then went to the vertical bandsaw and roughly cut out the shapes before taking them to the bench grinder and lastly a spindle sander for final shaping. This is after the first one was done.
-
Went back outside to test fit the pieces and with a small amount of hand filing to help the fit (thanks to a wandering drill bit) they fit nicely over the threaded posts.
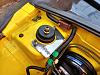
Once these fit the next step was to cut the upright support pieces. These were simple square shapes out of the same 3mm steel. One needed to be shorter than the other due to the asymmetrical nature of the mounting plate. I pre-drilled holes to use for alignment before I needed to open them to final size. I also cut two pieces of .5 inch round steel tube to use as mounting collars that would later be welded into the cross bar. I assembled these parts together to check spacing and measure what to cut the cross bar to.
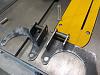
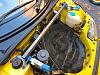
Once I had the approximate measurement, I cross drilled the square tube crossbar to the OD of the of the mounting collar tubes and then cut the crossbar directly in the middle of the hole. This left a semicircle that I could use to position the collars for welding.
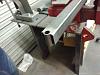
After welding I ground the welds on a disc sander to make the crossbar ends cleaner. Then I mounted them to the upright support pieces so I could position them in-situ on the car to tack them in place.
-
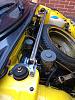
Then I prepped for welding on the car... the scary part. Covered everything even close, and disconnected the battery.
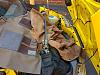
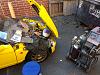
Tacked the pieces and then pulled them off to do the full welding. Not my prettiest welds ever given that I was using our old welder, but no excuses! I'm sure as I do more small pieces that will improve. Also didn't want to take the time to TIG everything since I am very slow with that, and not consistent at all. At least with the MIG I know I have good solid penetration and strong welds.
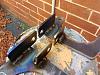
Next step was to cut and bend the torsional support for the mounting plates.
-
These then got welded and everything test fit again. Due to some warpage during welding I needed to slightly bend the plates back into shape, and open the mounting holes a tad. After I was sure everything fit well it was on to paint. Etching primer followed by high build primer to smooth things out a bit.
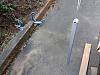
Then I painted everything matte black as a solid dark base. I left the mounting plates black and put a clear coat on them. Here you can see some slightly better welds that were the result of my boss bringing back the new welder right before I got done welding.
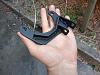
I found in our stores of paint some Mazda blue Perfect-Match by Duplicolor and thought it would look nice for the crossbar to have some color.
-
And after all that, here it is mounted in the car. I think it came out pretty well and it feels very solid. When driving the front end turn in feels a bit more crisp and a little of the body roll has been eliminated. I'm sure the addition of more bracing will make a larger difference as the body get stiffer. Still I think it is a good start and keeps me motivated to keep going.
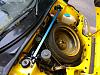
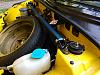
And of course since I made it myself I had to add a little YouTube swag from MightyCarMods since it passed the DIY test.
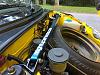
I'm excited to keep going and build more, and I will keep updating this thread when I make more pieces. Hope you all enjoy!
-
Nice work! I'm really looking forward to seeing what else you end up making!
If you check around on Yahoo Japan Auctions, there is one design that ties into the structure up front near the headlights as well. If you're so inclined, That would probably further help with rigidity.
Also, if you're up for making a version 2, consider extending the upright supports towards the centre of the car, and adding a second bolt like the OEM DC2 Type R bar. This should really ramp up torsional resistance from that member, since the joint there no longer acts as a pivot. Given the mass of the car and the forces the bar would likely be seeing (the towers are already part of the firewall, so I'm guessing comparatively low), you could probably replace the steel bar with an extruded rectangular aluminium tube and free up some weight.
-
Pro job. Consider adding slots to adjust camber. Probably too late..
Now that the top is more rigid. Consider fab an h for the bottom.
-
Thanks everyone for the advice and compliments! I do have a plan to make a triangular brace from the lower points near the headlight where the spare tire sheet metal support is mounted and back to the firewall with the bottom bolts of the hood latch mount. I could probably modify the current strut bar to add a second point of clamping on each end to eliminate the pivot, I will probably look into that after I get a couple more pieces done.
As for weight, I'm not too concerned right now with weight as I'm going to probably pull the spare tire and the sheet metal mount which will offset any additional weight added by using a steel bar over aluminum. Also, my aluminum welding skills definitely need practice so I'm not confident in fabricating a bar that won't crack under force like I am with steel. It is a future goal though to get good enough and replace parts with aluminum someday.
Plan for this weekend is to do a rear strut tower bar to get that evened out a little bit. Should be fun!
-
Don't worry about welding aluminium. The OEM bars are open ended (but internally braced) tubing bolted to steel plates.
Tags for this Thread
Posting Permissions
- You may not post new threads
- You may not post replies
- You may not post attachments
- You may not edit your posts
-
Forum Rules